Introduction to Metal Testing at Factories
In the world of manufacturing, the quality and integrity of products are paramount. One crucial aspect that directly impacts quality is the testing of metals used in production. Factories rely on precise metal testing techniques to ensure that their products meet industry standards and customer expectations.
Methods of Metal Testing for Quality Assurance
- Chemical Composition Analysis: Determining the exact chemical composition of metals is vital to assess their suitability for various applications. Techniques like Optical Emission Spectroscopy (OES) and X-Ray Fluorescence (XRF) provide accurate insights into the elemental composition of metals.
- Mechanical Testing: Understanding how metals will behave under stress or load is essential. Tensile, hardness, and impact tests help factories determine a metal’s strength, ductility, and resilience, guiding material selection and manufacturing processes.
- Non-Destructive Testing (NDT): NDT methods like ultrasonic, radiographic, and magnetic particle testing allow factories to evaluate metal properties without altering or damaging the material. These methods are particularly useful for inspecting finished products and identifying flaws.
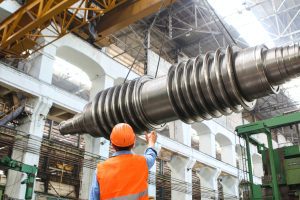
Importance of Accurate Metal Testing
Reliable metal testing plays a pivotal role in maintaining product quality, safety, and compliance. Using subpar or incorrectly characterized metals can lead to product failures, safety hazards, and legal repercussions. Accurate testing ensures that the chosen metals possess the desired attributes for their intended applications, enhancing overall product performance.
Benefits of Implementing Comprehensive Metal Testing
- Enhanced Product Quality: Thorough metal testing guarantees that the final products meet strict quality standards, resulting in increased customer satisfaction and loyalty.
- Cost Savings: Identifying unsuitable or substandard metals early in the production process prevents costly rework and recalls.
- Regulatory Compliance: Many industries must adhere to stringent regulations. Proper metal testing helps factories stay compliant with industry and safety standards.
- Innovation and Optimization: Comprehensive testing allows factories to explore new materials and optimize existing ones for better performance and efficiency.
In conclusion, metal testing at factories is a critical practice that directly influences the quality, safety, and performance of products. Employing accurate testing methods, such as chemical composition analysis, mechanical testing, and non-destructive testing, ensures that the chosen metals are well-suited for their intended applications. The importance of such testing cannot be overstated, as it leads to enhanced product quality, cost savings, regulatory compliance, and opportunities for innovation. As a trusted partner, we offer expertise in reliable metal testing that helps factories achieve superior results and maintain a competitive edge in the market.