These days, Japan has some of the most cutting edge companies in the world when it comes to advanced manufacturing and robots. As of 2022, Japanese companies made or created about 45% of all industrial robots in the world. This shows how far ahead of its time Japan is when it comes to automation technology. The $7.35 billion in record-breaking sales for industrial robots in 2022 show that more and more industries are committing to using advanced manufacturing technologies together. This piece talks about the issues, advantages, and possible outcomes of Japan’s advanced manufacturing and robotics scene in the coming years.
Trends in Japan’s Advanced Manufacturing Technology 2024
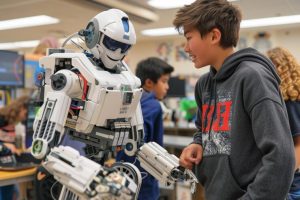
When it comes to Japan’s advanced manufacturing business, automation and robotics are very important. Companies are putting a lot of money into new tools because they need to be more efficient and productive. Logistics, food processing, and pharmaceuticals are some of the businesses that are moving more toward automation because they need to run more efficiently.
Current Patterns: Increased Automation:
It is now more common than ever for advanced robotics to be used in production. This trend is caused by the need for accuracy and consistency, which robots can provide more regularly than people. For instance, car factories have used robotics to automate assembly lines, which has led to faster production rates and fewer mistakes.
Integration of AI and Machine Learning:
Advanced manufacturing methods are rapidly embracing artificial intelligence (AI) and machine learning. These technologies allow robots to learn from their surroundings and gradually improve their performance over time. An example of this is the use of AI-powered robots in semiconductor manufacturing, where precision is critical.
Sustainability Initiatives:
With Japan’s aim to carbon neutrality, many manufacturers are using green technologies. This includes energy efficient machinery and environmentally friendly procedures that limit waste and effect. For example, businesses are investing in electric vehicles (EVs) and related technology as part of their manufacturing processes.
Japan is Starting to use Industrial Robots for Logistics.
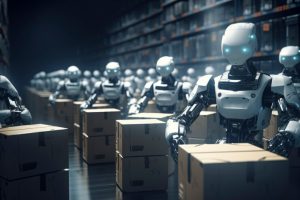
As Japan faces acute workforce shortages, the need for efficient logistics solutions has become increasingly pressing. The logistics sector is embracing automation to overcome these challenges, with robotics playing a central role.
Benefits of Robotics in Logistics
Increased Efficiency:
Automated robots can perform tasks such as picking, packing, and sorting goods much faster than human workers. This efficiency leads to shorter delivery times and increased throughput.
Cost Savings:
While the initial investment in robotics may be high, the long-term cost savings are significant. Robots reduce labor costs, minimize errors, and can operate continuously without breaks, leading to a faster return on investment.
Enhanced Safety:
In warehouses and distribution centers, robots can handle heavy lifting and hazardous materials, reducing the risk of workplace injuries. This focus on safety is crucial in maintaining a productive workforce.
Real-World Examples
One notable example of robotics adoption in logistics is the use of autonomous mobile robots (AMRs) in warehouses. Companies like Toyota Industries and Fanuc are leading the charge by integrating AMRs into their operations. These robots navigate complex warehouse environments, transporting goods efficiently and effectively.
Japan’s Market for Automation in Packaging and Transport
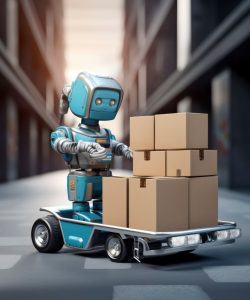
The packaging and transport sectors are also experiencing significant advancements due to automation. The integration of robotics into these processes is transforming how goods are packaged, labeled, and transported.
Benefits of Automation in Packaging and Transport
Precision and Consistency:
Automated packaging systems ensure that products are packaged consistently, reducing the risk of errors that can occur with manual processes.
Scalability:
As demand fluctuates, automated systems can easily scale operations up or down, allowing companies to respond quickly to market changes.
Data Collection and Analysis:
Automated systems can collect valuable data on packaging processes, enabling manufacturers to analyze performance and identify areas for improvement.
Case Study
A prominent example of automation in packaging is the collaboration between Seiko Epson Corporation and several leading manufacturers to develop state-of-the-art packaging solutions. Their automated systems are designed to handle everything from food packaging to electronics, ensuring high efficiency and minimal waste.
Impact of Workforce Shortages on Japanese Manufacturing
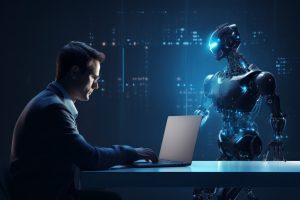
Japan’s aging population presents significant challenges for the workforce, driving the need for advanced manufacturing technologies. The country’s workforce has declined by more than 2.7 million in the past decade, and projections indicate a potential 40% decrease by 2065.
Addressing Workforce Shortages
- Robotics as a Solution: With a decreasing labor pool, manufacturers are increasingly turning to robotics to maintain productivity. Robots can fill gaps left by human workers, ensuring that production continues unabated.
- Enhanced Training: Companies are also investing in training programs to equip existing workers with the skills needed to operate advanced manufacturing technologies, bridging the gap between human labor and automation.
Government Support for Advanced Manufacturing in Japan
The Japanese government plays a crucial role in fostering innovation in the manufacturing sector. In its fiscal year 2023 budget, the government allocated $39.3 billion to support supply chain resiliency and the upgrading of manufacturing facilities.
Benefits of Government Support
- Subsidies for Technology Upgrades: Manufacturers can apply for government subsidies to modernize their equipment, enabling them to remain competitive in a rapidly changing market.
- Investment in Research and Development: Government support encourages innovation by funding research and development initiatives, paving the way for groundbreaking technologies in manufacturing.
Example of Government Initiatives
The “Manufacturing Innovation Strategy” launched by the Japanese government aims to enhance competitiveness in the manufacturing sector. This initiative encourages collaboration between academia, industry, and government to develop cutting-edge technologies.
Digital Infrastructure Investment in Japan’s Manufacturing Sector
As part of its growth strategy, Japan’s manufacturing sector is expected to invest significantly in digital infrastructure. Companies are estimated to spend $4.1 billion on digital infrastructure by 2030, up from below $1 billion currently.
Benefits of Digital Infrastructure
- Improved Connectivity: Enhanced digital infrastructure enables real-time communication between machines, improving coordination and efficiency in manufacturing processes.
- Data-Driven Decision Making: Companies can leverage data analytics to gain insights into their operations, leading to informed decision-making and optimized processes.
- Enhanced Cybersecurity: As manufacturing becomes more digital, robust cybersecurity measures become essential to protect sensitive data and systems from cyber threats.
Real-World Application
Companies like Hitachi and Fujitsu are leading the way in digital transformation within the manufacturing sector. They are developing advanced systems that integrate IoT (Internet of Things) technologies, enabling manufacturers to monitor and control their processes remotely.
Trade Opportunities for U.S. Companies in Japan’s Robotics Market
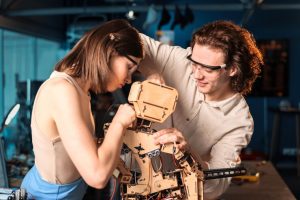
The growing demand for advanced manufacturing technologies in Japan presents lucrative opportunities for U.S. solutions providers. Partnering with local agents or distributors can be a key strategy for success.
Benefits of Collaborating with Local Partners
- Access to Established Networks: Local partners possess invaluable market knowledge and established relationships, enabling U.S. companies to navigate the Japanese market more effectively.
- Cultural Insights: Understanding cultural nuances is crucial for success in Japan. Local partners can provide insights into consumer behavior and preferences.
- Streamlined Market Entry: Collaborating with established firms can expedite the market entry process, allowing U.S. companies to launch their products and services more efficiently.
Example of Successful Partnerships
Several U.S. robotics companies, including Boston Dynamics and Universal Robots, have successfully entered the Japanese market by collaborating with local distributors. These partnerships have facilitated the introduction of innovative robotics solutions tailored to meet Japanese industry needs.
Factory Innovation Week 2024: A Platform for Advancement
Factory Innovation Week will be held in Tokyo from January 24th to 26th, 2024. It is a big event for people who work in the business. It takes place at the same time as Nepcon Japan and Smart Logistics Japan, which makes it simple to meet new people and see the newest robots and industrial technology.
Benefits of Participating in Factory Innovation Week
- Networking Opportunities: Attendees can connect with key industry players, potential partners, and customers, fostering collaboration and innovation.
- Exposure to Cutting-Edge Technologies: The event showcases the latest technologies in manufacturing and robotics, allowing participants to stay updated on industry trends.
- Workshops and Seminars: Factory Innovation Week features educational sessions that provide insights into best practices and emerging trends in advanced manufacturing.
Final Thought
Japan’s advanced manufacturing and robotics market is very active and changing very quickly. This is because of new technologies and the urgent need to solve worker problems. As the country puts money into digital and automated infrastructure, there are huge chances for people to work together and come up with new ideas. If U.S. companies want to get into this market, they should think about strategic relationships and keep up with the latest news and trends. Japan is working to become more productive, environmentally friendly, and technologically advanced around the world. Businesses can help by accepting the future of manufacturing.