3D manufacturing, also known as additive manufacturing, has emerged as a transformative technology across industries, fundamentally altering how products are designed, produced, and distributed. In this process, a digital model is used to create three-dimensional objects layer by layer, offering significant advantages over traditional subtractive manufacturing. From custom prosthetics in healthcare to lightweight components for aerospace, 3D printing is ushering in a new era of efficiency, precision, and sustainability.
In this article, we explore the latest advancements, industry applications, and technological innovations in 3D manufacturing. We also discuss the challenges it faces, regulatory considerations, and the future trajectory of this rapidly evolving field.
Advancements in 3D Printing Materials
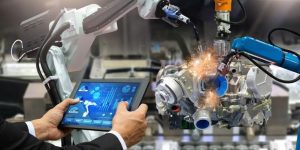
One of the most exciting aspects of 3D manufacturing is the constant innovation in materials. Traditional 3D printing was largely limited to plastics, but today, manufacturers can use a wide array of materials, including metals, composites, bio-inspired substances, and even sustainable bioplastics.
Metal 3D Printing
Metal 3D printing has grown tremendously, with industries such as aerospace, automotive, and medical devices reaping the benefits. Technologies like Selective Laser Melting (SLM) and Direct Energy Deposition (DED) are enabling the creation of metal parts with high precision and structural integrity. For example, GE Aviation uses 3D printing to produce lightweight, high-performance metal components for jet engines. The ability to print complex geometries, which were once too difficult or costly to manufacture, has revolutionized the production of critical aerospace parts.
Sustainable Materials
As environmental concerns grow, there is an increasing focus on using sustainable materials in 3D printing. Biodegradable plastics, such as PLA (Polylactic Acid), and recycled materials are gaining traction, particularly in consumer goods and packaging. Companies like Materialise are developing eco-friendly filaments that reduce plastic waste while still delivering strong, durable printed parts.
A notable example of sustainable 3D printing is Carbon’s development of EPU (Elastic Polyurethane), a 3D printing material designed for sustainable manufacturing in industries like automotive and consumer products.
Bio-Inspired Materials
Bio-inspired materials, designed to mimic natural structures, are pushing the boundaries of material science. By leveraging nature’s inherent efficiency, these materials often offer improved strength-to-weight ratios, flexibility, and durability. For instance, researchers at MIT have designed materials inspired by the honeycomb structure found in nature, resulting in lighter, more efficient 3D printed components.
Applications in Various Industries
The potential applications of 3D manufacturing span across nearly every sector, with transformative results.
Aerospace
In aerospace, 3D printing is reducing the weight of aircraft and increasing fuel efficiency. Boeing and Airbus use 3D printing to create complex, lightweight parts such as engine components, air ducts, and brackets. NASA has even developed a 3D printing system capable of producing rocket components in space, reducing the need for resupply missions.
A landmark case study involves GE Aviation, which has used 3D printing to produce more than 30,000 fuel nozzles for its LEAP jet engines. These nozzles, made of advanced metal alloys, are 25% lighter and five times more durable than their traditionally manufactured counterparts.
Automotive

In the automotive industry, 3D printing is not only used for prototyping but also for the production of end-use parts. BMW, for example, uses 3D printing to create personalized and customized vehicle parts. By using lightweight, durable materials, BMW reduces the weight of their cars and enhances performance.
Ford has implemented 3D printing for manufacturing complex parts and creating tooling solutions. In fact, 3D printing enabled Ford to significantly reduce production time for prototypes, leading to faster vehicle development cycles.
Healthcare
In healthcare, 3D printing has been revolutionary in the development of custom prosthetics, implants, and surgical tools. For example, Stratasys and Materialise have collaborated with hospitals to produce custom prosthetics tailored to individual patients, providing a higher level of comfort and functionality than traditional options.
A particularly exciting application is bioprinting, where researchers are working toward printing human tissues and organs. While still in its infancy, companies like Organovo are advancing the field by creating 3D-printed liver tissues for drug testing, potentially leading to breakthroughs in organ transplantation.
3D printing is reshaping how buildings are designed and constructed. ICON, a Texas-based construction technology company, has developed a 3D printer that can print entire homes in a matter of days. These 3D-printed homes, made with a specialized concrete-like material, are not only faster to build but also more affordable and sustainable, potentially addressing housing shortages in low-income areas.
A landmark example is the Apis Cor project in Dubai, where a 3D printer constructed a fully functional 6,900-square-foot building, showcasing the potential of 3D printing in large-scale construction.
Technological Innovations in 3D Manufacturing
The technology behind 3D manufacturing continues to evolve rapidly. Key innovations are driving improvements in speed, material diversity, and precision.
Artificial Intelligence (AI) and Machine Learning
AI and machine learning are playing an increasingly important role in optimizing 3D printing processes. AI algorithms can predict how a part will behave during production, adjusting parameters in real-time to prevent defects. Siemens, for example, uses AI to optimize the design and printing processes, ensuring better material utilization and reducing errors.
Hybrid Manufacturing
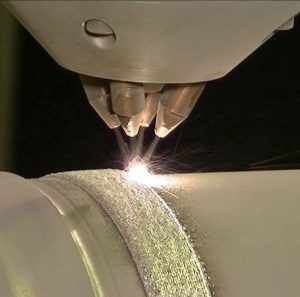
Hybrid manufacturing is the integration of 3D printing with traditional subtractive methods, such as CNC machining. This approach allows manufacturers to take advantage of the speed and customization of 3D printing while achieving the high precision and finish of traditional techniques. Companies like DMG Mori and Mazak are leading the development of hybrid machines that combine 3D printing with machining capabilities, creating parts with both complex geometries and superior surface finishes.
Multi-Material Printing
Multi-material 3D printing allows for the creation of parts with multiple properties in a single build process. This is particularly useful in industries where products require a combination of rigid and flexible components. For instance, Stratasys has developed multi-material 3D printing technology that enables engineers to create prototypes with a variety of materials, such as rigid plastics and soft elastomers, all in one print.
Speed and Scalability in 3D Printing
While traditional 3D printing methods were slow and mainly suited for prototyping, recent advancements are making 3D printing a viable option for mass production.
Faster Printing Technologies
Technologies such as Continuous Liquid Interface Production (CLIP) and Multi Jet Fusion (MJF) have significantly sped up the printing process. Carbon’s CLIP technology uses light and oxygen to cure photopolymer resin in continuous layers, enabling the rapid production of parts. This has been particularly useful in industries like footwear, where companies like Adidas use 3D printing to create mass-customized shoes.
HP’s Multi Jet Fusion technology, on the other hand, enables the printing of high-quality functional parts at a faster rate than traditional 3D printers. This method is ideal for industrial applications where speed and scalability are crucial.
Mass Production with 3D Printing
The transition from prototyping to mass production is one of the most promising developments in 3D manufacturing. Companies are now using 3D printing to produce parts in high volumes. Volkswagen, for example, has started using 3D printing for producing spare parts in small batches, reducing inventory costs and enabling faster replacements.
Decentralized Manufacturing
The decentralization of manufacturing is another significant advantage of 3D printing. By enabling local production of parts, 3D printing reduces the need for long supply chains and lowers transportation costs. This model also allows for more agile and flexible manufacturing, making it easier to adapt to changing market demands.
Cloud-Based 3D Printing and Digital Supply Chains
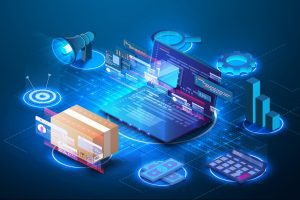
With the growing adoption of 3D printing, cloud platforms are becoming crucial for managing print jobs and coordinating production across multiple locations.
Cloud-Based 3D Printing
Cloud-based 3D printing platforms allow businesses to store and access digital models from anywhere in the world. These platforms enable remote management and control of printers, ensuring that print jobs are completed efficiently. For example, Autodesk’s Fusion 360 platform integrates design and simulation tools with cloud-based 3D printing, enabling companies to design and manufacture products seamlessly.
Digital Supply Chains
Digital supply chains are becoming increasingly important in the context of 3D printing. Through the use of digital twins, companies can create a virtual replica of a physical object, allowing them to test, simulate, and refine designs before actual production. This streamlines the manufacturing process, reducing time-to-market and costs.
Regulatory and Certification Developments
As 3D printing becomes more widespread, regulatory frameworks are being developed to ensure the safety and quality of 3D printed parts, especially in critical sectors like aerospace and healthcare.
Regulation in Aerospace and Healthcare
The FAA (Federal Aviation Administration) has established guidelines for certifying 3D printed parts in aviation, particularly in ensuring the structural integrity and performance of components. Similarly, the FDA has been developing regulations for 3D printed medical devices and implants, ensuring that these products meet safety and quality standards.
Intellectual Property (IP) Challenges
The proliferation of 3D printing also raises questions about intellectual property protection. Because 3D printers allow users to replicate designs easily, companies are exploring new ways to protect their patents and copyrights. Digital rights management (DRM) solutions are being integrated into 3D printing systems to prevent unauthorized replication of proprietary designs.
Challenges and Future Directions in 3D Manufacturing
Despite its rapid growth, 3D printing faces several challenges, including post-processing bottlenecks, high energy consumption, and barriers to adoption in emerging markets.
Post-Processing Bottleneck
Post-processing remains one of the most time-consuming aspects of 3D printing. While the printing process itself has become faster and more efficient, the cleaning, curing, and finishing of printed parts can still take significant time and labor. Innovations in automated post-processing systems are expected to address these bottlenecks.
Energy Consumption
3D printing, especially with metal and resin-based technologies, can be energy-intensive. To mitigate the environmental impact, researchers are exploring ways to make the process more energy-efficient and sustainable. Companies are also turning to renewable energy sources to power 3D printers, reducing their carbon footprint.
Global Adoption
While 3D printing is well-established in developed countries, adoption in emerging markets remains slower. Cost, infrastructure, and skill gaps present significant barriers. However, as the technology continues to become more affordable and accessible, global adoption is expected to rise, particularly in regions with manufacturing-driven economies.
Conclusion
The future of 3D manufacturing is undeniably promising. With continuous advancements in materials, speed, scalability, and applications across industries, 3D printing is revolutionizing how products are designed, produced, and delivered. From aerospace to healthcare, 3D manufacturing is unlocking new possibilities and efficiencies that were previously unimaginable.
As the technology matures, it will continue to disrupt traditional manufacturing, offering more sustainable, cost-effective, and personalized solutions. However, addressing challenges such as post-processing, energy consumption, and IP protection will be critical for the full realization of its potential.
Ultimately, 3D manufacturing is not just a technological trend—it is the foundation of the future of production. As it evolves, it promises to redefine how we create, innovate, and consume.