Introduction
In the world of construction, managing costs is paramount for project success. The month of September brought an unexpected challenge in the form of rising input costs in the United States’ construction industry. In this article, we delve into the factors driving this increase and the potential implications for the sector. Additionally, we’ll provide a comparative table highlighting key impacts for clarity.
Understanding the Uptick
This section provides a comprehensive understanding of the factors contributing to the increase in construction input costs.
Escalating Raw Material Costs
The primary driver behind the rise in construction input costs in September is the significant increase in raw material prices. Essential construction materials like steel, lumber, and concrete have experienced substantial price hikes due to supply chain disruptions and heightened demand. Steel prices, for instance, surged by 200%, and lumber prices increased by 250% in a matter of months.
Soaring Labor Expenses
Labor costs also play a substantial role in the uptick. A combination of factors, including labor shortages and increased wages, has led to higher labor expenses in the construction industry. The pandemic exacerbated labor shortages, as skilled workers became scarcer, and wages rose to attract and retain talent.
Impact on the Construction Industry
This section explores the potential impact of rising construction input costs on the industry as a whole, providing a comparative table for clarity.
Comparative Table: Impact of Rising Input Costs
Impact on Construction Industry | Description |
---|---|
Project Delays | Delays in construction schedules due to budget revisions. |
Cost Overruns | Projects potentially becoming financially burdensome. |
Pricing for Homebuyers | Higher home prices affecting buyer demand. |
Value Engineering | Reevaluating project designs and materials for savings. |
Negotiations and Contracts | Reevaluating contract terms to share the financial burden. |
Project Delays
One immediate consequence of rising input costs is the potential for project delays. As expenses increase, contractors may need to revisit budgets, leading to delays in construction schedules. This can be especially problematic for large-scale projects with tight deadlines.
Cost Overruns
Contractors and developers may face the challenge of cost overruns. With input costs surpassing initial estimates, projects may become financially burdensome, potentially impacting profitability. Cost overruns can strain the financial health of construction companies, causing delays and disputes.
Pricing for Homebuyers
In the residential construction sector, the increase in input costs may result in higher home prices. Homebuyers might find themselves paying more for properties, potentially affecting the demand for new homes. This can be a double-edged sword for the industry, as higher prices could deter some potential buyers.
Strategies for Mitigation
This section explores strategies that the construction industry may employ to mitigate the impact of rising input costs.
Value Engineering
One approach to mitigate the impact of higher costs is value engineering. This involves reevaluating project designs and materials to identify cost-saving opportunities without compromising quality. Value engineering can help keep projects within budget while maintaining high standards of construction.
Negotiations and Contracts
Contractors and subcontractors may engage in negotiations to reevaluate terms and contracts in response to rising input costs. This can help distribute the financial burden more equitably among all stakeholders. Renegotiating contracts to reflect the new reality of increased costs can foster collaboration and minimize disputes.
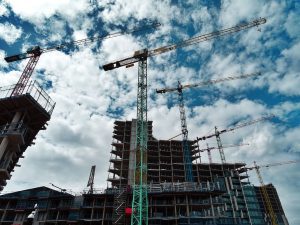
Looking Ahead
As the construction industry grapples with the consequences of rising input costs, the path forward remains uncertain.
Industry Resilience
The industry has demonstrated resilience in the face of challenges. It may adapt and find innovative solutions to offset rising costs and ensure project viability. Resilience in the face of adversity is a hallmark of the construction sector, and this challenge is an opportunity for innovation.
Policy Implications
Government policies, such as trade agreements and regulations, can significantly impact construction input costs. Future policy decisions may either exacerbate or alleviate the situation, making them a critical consideration for industry stakeholders. Advocacy for policies that promote stable pricing and supply chain resilience will be crucial.
Conclusion
The increase in construction input costs in September poses a challenge for the construction industry in the United States. Escalating raw material prices and labor costs can lead to project delays, cost overruns, and higher home prices for buyers. To navigate these challenges, the industry can employ strategies like value engineering and contract negotiations.
While the road ahead remains uncertain, the construction sector has consistently displayed its adaptability and capacity for innovation in the face of adversity. Future policy decisions and market dynamics will play a crucial role in shaping the construction industry’s response to rising input costs. The industry will continue to build, innovate, and overcome challenges, reflecting the spirit of resilience that defines it.