The evolution of 3D printing materials has been nothing short of revolutionary, offering diverse material options for various industries. Initially, 3D printing was limited to basic plastics, but advancements have expanded the range to include metals, ceramics, and even biological materials. This diversity enables industries such as aerospace, automotive, healthcare, and consumer goods to leverage 3D printing for a wide array of applications. For instance, aerospace companies can now print lightweight metal components, while the healthcare sector can create biocompatible implants and prosthetics. The availability of these diverse materials has significantly broadened the scope and utility of 3D printing across different sectors.
Moreover, 3D printing has enhanced material properties for specialized applications, making it possible to create objects with tailored characteristics. Engineers and scientists can now design materials with specific mechanical, thermal, and electrical properties to meet the unique demands of specialized applications. For example, in the medical field, materials can be engineered to be bioresorbable, allowing implants to gradually dissolve in the body without the need for surgical removal. In the automotive industry, materials can be developed to withstand high temperatures and stresses, ensuring durability and performance. These advancements in material properties are pushing the boundaries of what can be achieved with 3D printing, opening up new possibilities for innovation and development.
Integration with AI and IoT
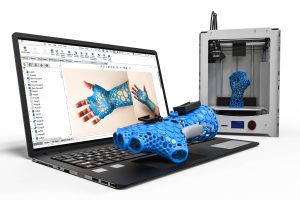
The integration of 3D printing with artificial intelligence (AI) and the Internet of Things (IoT) is enhancing precision manufacturing. AI algorithms can optimize the design and printing process, ensuring that each layer of material is deposited with utmost accuracy. This level of precision is particularly important for complex and intricate designs, where even the slightest error can compromise the integrity of the final product. AI can also predict and prevent potential issues during the printing process, reducing waste and improving efficiency. The combination of AI and 3D printing is transforming manufacturing into a highly precise and efficient endeavor.
Additionally, IoT integration allows for real-time monitoring and control of stereolithography processes. Sensors embedded in 3D printers can collect data on various parameters such as temperature, humidity, and material flow rate. This data can be transmitted to a central system, where it is analyzed to ensure optimal printing conditions. IoT-enabled 3D printers can also be remotely controlled, allowing operators to make adjustments on the fly. This real-time monitoring and control capability enhances the reliability and consistency of 3D printing, making it a more viable option for large-scale manufacturing.
Speed and Precision Improvements
One of the most significant advantages of 3D printing is its ability to drastically reduce manufacturing time and enhance speed. Traditional manufacturing methods often involve multiple steps, including tooling, machining, and assembly, which can be time-consuming. In contrast, 3D printing can produce a complete object in a single step, significantly shortening the production cycle. This rapid manufacturing capability is particularly beneficial for industries that require quick turnaround times, such as aerospace and automotive. By reducing manufacturing time, 3D printing allows companies to respond more quickly to market demands and stay competitive.
Furthermore, 3D printing offers unparalleled precision in complex and intricate designs. Traditional manufacturing methods can struggle with intricate geometries and fine details, often requiring additional processing steps to achieve the desired level of precision. Stereolithography on the other hand, can produce highly detailed and accurate objects directly from digital designs. This precision is invaluable for applications such as medical devices, where exact dimensions and intricate features are critical for functionality. The ability to achieve such high levels of precision makes stereolithography an ideal solution for producing complex and customized components.
Decentralized Manufacturing
3D printing enables localized, on-demand production, which is a significant shift from traditional centralized manufacturing. With 3D printing, products can manufactured close to the point of use, reducing the need for extensive supply chains and transportation. This localized production capability is particularly advantageous for remote or underserved areas, where access to manufactured goods can be limited. By enabling on-demand production, 3D printing allows for greater flexibility and responsiveness to local needs, reducing lead times and minimizing inventory costs.
Additionally, 3D printing reduces reliance on centralized manufacturing hubs, which can be vulnerable to disruptions such as natural disasters, political instability, or supply chain issues. Decentralized manufacturing with stereolithography distributes production capabilities across multiple locations, enhancing resilience and reducing the risk of supply chain disruptions. This decentralized approach also supports sustainability efforts by reducing the carbon footprint associated with transportation and logistics. By enabling more localized and resilient manufacturing, 3D printing is reshaping the global manufacturing landscape.
Prototyping and Product Development
3D printing accelerates prototyping and product development cycles, allowing companies to bring new products to market more quickly. Traditional prototyping methods often involve multiple iterations and can be time-consuming and costly. In contrast, 3D printing allows for rapid prototyping, enabling designers to create and test multiple versions of a product in a short period. This accelerated prototyping process allows for faster identification of design flaws and improvements, reducing the time and cost associated with product development.
Moreover, stereolithography enables rapid iteration and innovation in manufacturing. Designers and engineers can quickly modify digital designs and produce new prototypes, fostering a culture of continuous improvement and innovation. This iterative process is particularly valuable for industries such as consumer electronics, where product lifecycles are short, and innovation is key to staying competitive. By facilitating rapid iteration and innovation, 3D printing is driving the development of new and improved products across various industries.
Healthcare and Bioprinting
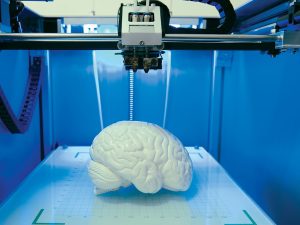
3D printing is revolutionizing personalized healthcare solutions, offering customized medical devices and implants tailored to individual patients. Traditional medical devices are often produced in standard sizes, which may not fit all patients perfectly. 3D printing allows for the creation of bespoke devices that match the unique anatomy of each patient, improving comfort and effectiveness. For example, custom 3D-printed prosthetics can provide a better fit and greater functionality for amputees. Similarly, patient-specific surgical guides can enhance precision in complex procedures, reducing the risk of complications.
Furthermore, bioprinting is an emerging field within 3D printing that holds the potential to create organs for transplant and medical research. Bioprinting involves the layer-by-layer deposition of bioink, which contains living cells, to create tissue-like structures. Researchers are exploring the use of bioprinting to produce functional organs such as kidneys, livers, and hearts, which could address the critical shortage of donor organs. Additionally, bioprinted tissues can used for drug testing and medical research, providing a more accurate model of human biology than traditional methods. The advancements in bioprinting poised to transform the field of regenerative medicine and improve patient outcomes.
Automotive and Aerospace Applications
3D Printing is reducing production time in automotive manufacturing, enabling faster development and production of components. Traditional manufacturing methods for automotive parts often involve complex tooling and machining processes, which can be time-consuming and costly. 3D printing allows for the direct production of parts from digital designs, eliminating the need for tooling and reducing lead times. This capability is particularly valuable for producing custom or low-volume parts, where traditional methods may not be cost-effective. By reducing production time, 3D printing allows automotive manufacturers to bring new models to market more quickly and respond to changing customer demands.
Additionally, 3D printing is customizing aerospace components for enhanced performance. The aerospace industry demands high-performance components that are lightweight, durable, and capable of withstanding extreme conditions. Stereolithography allows for the creation of complex geometries and optimized designs that are difficult or impossible to achieve with traditional manufacturing methods. For example, 3D-printed components can designed with internal lattice structures that provide strength while minimizing weight. This customization capability enhances the performance and efficiency of aerospace components, contributing to the development of more advanced and fuel-efficient aircraft.
Education and Skill Development
3D printing is revolutionizing educational tools and resources, providing students with hands-on learning experiences. Traditional educational methods often rely on textbooks and lectures, which can be limiting in terms of practical application. 3D printing allows students to create physical models of concepts they are learning, enhancing their understanding and engagement. For example, students studying engineering can design and print prototypes of their projects, gaining valuable experience in the design and manufacturing process. Similarly, medical students can use 3D-printed anatomical models for hands-on practice, improving their skills and confidence.
Moreover, 3D printing is enhancing hands-on skill development in manufacturing. As the technology becomes more prevalent in the industry, there is a growing demand for skilled professionals who can operate and maintain 3D printers. Educational institutions are incorporating stereolithography into their curricula to prepare students for careers in advanced manufacturing. By providing students with practical experience in 3D printing, these programs are equipping the next generation of workers with the skills needed to succeed in the evolving manufacturing landscape. The integration of 3D printing in education is fostering innovation and preparing students for the future of work.
Economic Implications
3D printing reduces manufacturing costs significantly, offering a cost-effective alternative to traditional manufacturing methods. Traditional manufacturing often involves high upfront costs for tooling and setup, which can be prohibitive for small-scale production. In contrast, stereolithography eliminates the need for tooling and allows for the direct production of parts from digital designs, reducing costs. Additionally, stereolithography minimizes material waste, as it only uses the material needed to create the object. This cost-saving capability is particularly beneficial for small and medium-sized enterprises (SMEs) that may not have the resources for large-scale production.
Furthermore, 3D printing accelerates time-to-market for new products, providing a competitive advantage for companies. The ability to rapidly prototype and produce parts allows companies to bring new products to market more quickly, responding to customer demands and market trends. This accelerated time-to-market is particularly valuable in industries with fast-paced innovation cycles, such as consumer electronics and fashion. By reducing the time and cost associated with product development and production, 3D printing enables companies to stay ahead of the competition and capitalize on new opportunities.
Consumer Market Growth
3D printing drives personalized consumer product innovation, allowing for the creation of customized products tailored to individual preferences. Traditional mass production methods often result in standardized products that may not meet the unique needs of every consumer. 3D printing allows for the customization of products, such as personalized jewelry, footwear, and home decor, providing a more personalized consumer experience. This customization capability is driving innovation in the consumer market, as companies explore new ways to meet the diverse needs and preferences of their customers.
Additionally, 3D printing enables cost-effective small batch manufacturing, providing an alternative to large-scale production. Traditional manufacturing methods often require large production runs to be cost-effective, which can be limiting for niche or specialized products. stereolithography allows for the production of small batches of products without the need for expensive tooling or setup. This capability is particularly valuable for startups and small businesses, which can produce limited quantities of products to test the market without significant financial risk. By enabling cost-effective small batch manufacturing, 3D printing is empowering entrepreneurs and driving growth in the consumer market.