3D Printing in the Automotive Industry: Revolutionizing Manufacturing and Design
The automotive industry has always been at the forefront of technological innovation. As competition rises, manufacturers are constantly seeking ways to develop faster, more efficient, and cost-effective production methods. One technology that’s driving this transformation is 3D printing, also known as additive manufacturing. From prototyping to the production of end-use parts, 3D printing is revolutionizing the way vehicles are designed and manufactured.
What is 3D Printing in the Automotive Industry?
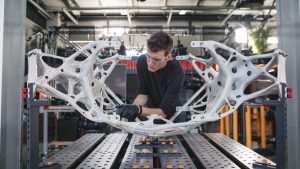
3D printing in the automotive sector refers to the process of creating three-dimensional components by layering materials such as plastics, metals, and composites. This technology enables manufacturers to produce parts directly from digital designs, offering a more flexible and efficient approach to car manufacturing.
The Benefits of 3D Printing in Automotive Manufacturing
The automotive industry leverages 3D printing for numerous reasons. Let’s explore some of the key benefits:
1. Faster Product Development
Rapid Prototyping:
One of the major advantages of 3D printing is its ability to accelerate product development through rapid prototyping. Traditional prototyping methods involve a lengthy process of designing, tooling, and testing. In contrast, 3D printing allows manufacturers to quickly produce multiple design iterations, test them for fit and function, and make necessary adjustments without significant delays. This reduces the time-to-market for new models and innovations.
Cost-Effective Production:
By eliminating the need for extensive tooling, manufacturers can lower production costs. This makes 3D printing a cost-effective option, especially for small batch production runs and prototyping phases.
2. Greater Design Flexibility
The flexibility of 3D printing allows automotive designers to experiment with multiple design concepts simultaneously. Engineers can easily modify designs, improve features, and optimize parts without major changes to the production line.
This level of flexibility is particularly beneficial in the motorsports and luxury car segments, where customization and design innovation are key.
3. Customization
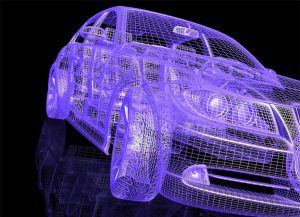
In the automotive industry, customization plays a significant role, especially within the luxury and high-performance vehicle markets. 3D printing allows automakers to create personalized parts that match specific customer preferences, whether it’s for the interior or exterior of a vehicle.
For instance, Porsche has utilized 3D printing to produce customized bucket seats with varying levels of firmness to enhance comfort and performance for individual drivers. This approach not only improves the driving experience but also creates a more exclusive offering for customers.
4. Production of Complex Geometries
3D printing enables manufacturers to produce parts with intricate designs and complex geometries that would be difficult or impossible to create using traditional manufacturing methods. This includes components with internal channels, thin walls, and fine meshes, which are essential for applications like conformal cooling.
The ability to create lightweight yet durable parts also makes 3D printing an ideal solution for reducing overall vehicle weight, thus improving fuel efficiency and performance.
5. On-Demand Manufacturing
Additive manufacturing allows manufacturers to produce spare parts on demand, reducing the need for large inventories. This approach ensures that parts are manufactured only when needed, resulting in lower storage costs and faster delivery times.
Porsche, for example, has used 3D printing to produce spare parts for its classic cars, addressing the challenge of limited production runs and rare parts availability.
6. Tooling Efficiency
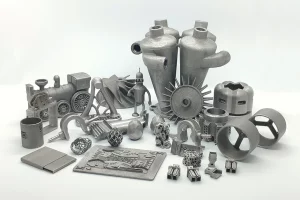
Tooling is an essential aspect of automotive manufacturing, involving jigs, fixtures, and molds used for assembling parts. 3D printing makes it possible to produce tooling aids at a fraction of the cost compared to traditional methods.
Ford Motor Company has demonstrated this benefit by using 3D printing to create an assembly lift assist. This 3D-printed tool was 50% lighter than its conventional counterpart, making it easier to handle and reducing repetitive motion injuries for assembly workers.
Real-World Examples of 3D Printing in the Automotive Industry
1. Porsche’s 3D-Printed Seats
Porsche has been a pioneer in integrating 3D printing into its production process. The German automaker has developed customized 3D-printed seats that offer varying levels of firmness and better ergonomics. This innovation draws inspiration from motorsport seats, which are tailored to the driver’s body shape.
Case Study: Porsche’s Custom Bucket Seats
In 2020, Porsche announced plans to develop 3D-printed bucket seats that offer a personalized fit based on the driver’s body contours. The prototype seats, tested on European race tracks, featured three different firmness levels: hard, medium, and soft. The results from customer feedback were used to develop the final version for commercial use in 2021. This project exemplifies how 3D printing can enhance both performance and comfort.
2. BMW’s 3D-Printed Roof Bracket
BMW has embraced 3D printing for various automotive applications, including end-use parts. In the development of its i8 Roadster, BMW created a metal roof bracket using 3D printing. This bracket weighs 44% less than its traditionally manufactured counterpart, demonstrating the potential of additive manufacturing to produce lightweight and efficient components.
Case Study: BMW’s Additive Manufacturing Initiative
BMW’s Additive Manufacturing Campus, launched in 2020, has produced over 1 million parts using 3D printing. The facility focuses on developing lightweight components for both production and prototype models, showcasing the potential for large-scale additive manufacturing in the automotive sector.
3. Ford’s Use of 3D Printing for Tooling
Ford Motor Company has successfully integrated 3D printing into its tooling processes, using it to develop custom tools and fixtures that enhance manufacturing efficiency.
Case Study: Ford’s Lift Assist
In 2018, Ford was awarded for its use of 3D printing in tooling. The development of the 3D-printed lift assist reduced production costs by 50% and improved safety by creating a lighter tool that reduces worker strain. This innovation underscores the potential of 3D printing to improve factory operations.
4. On-Demand Spare Parts by Porsche
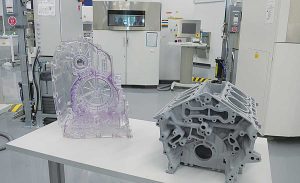
Porsche has adopted additive manufacturing to produce on-demand spare parts for its classic cars, which often have low production volumes and limited part availability. By using SLM (Selective Laser Melting) for metal parts and SLS (Selective Laser Sintering) for plastic components, Porsche has reduced the cost and time required to produce rare parts.
Case Study: 3D-Printed Classic Car Parts
In early 2018, Porsche announced that it would use 3D printing to produce more than 20 spare parts for classic models. The use of additive manufacturing has not only allowed Porsche to meet the demand for these parts but has also helped in preserving the legacy of its historic vehicles.
The Future of 3D Printing in Automotive Manufacturing
The future of 3D printing in the automotive industry looks promising, with advancements in printer speed, material variety, and printing capabilities paving the way for broader adoption. Here’s how 3D printing is set to evolve in the coming years:
1. Integration in Mass Production
Although 3D printing has been primarily used for prototyping and small-scale production, improvements in industrial printers and materials are making it a viable option for mass production. For instance, BMW has been able to produce up to 238 metal roof brackets per printing cycle, hinting at the potential for larger production runs.
2. Customization on a Larger Scale
Automakers are expected to expand their use of 3D printing to offer broader customization options, allowing customers to personalize not only the aesthetics but also the performance characteristics of their vehicles. This level of personalization would be impossible with conventional manufacturing methods.
3. Sustainability Initiatives
As sustainability becomes a priority for automakers, 3D printing offers a more environmentally friendly approach. By producing parts only when needed and reducing material waste, manufacturers can minimize their carbon footprint. This aligns with the industry’s goal of achieving more sustainable production processes.
Conclusion
3D printing is transforming the automotive industry by enabling faster development, greater flexibility, and increased customization. From rapid prototyping to end-use parts and tooling, the technology provides cost-effective solutions that enhance design innovation and operational efficiency. As the technology continues to advance, it will likely play an even bigger role in mass production, on-demand manufacturing, and sustainable development. By embracing 3D printing, automakers can remain competitive, reduce costs, and meet the evolving demands of modern consumers.